It is 2030 and the factory of the future has sensors everywhere and predictive maintenance will be the norm. Big Data in manufacturing will truly be king and simulations will drive decision making. New business models will help to share data while protecting intellectual property. This will be industry 5.0.
Human-machine cooperation in 2030 will be possible only because of emerging technologies that are already shaping the manufacturing industry.
Emerging Technologies that will disrupt manufacturing
Over the next decade, 4 million manufacturing jobs are expected to be filled by highly skilled workers. Out of which, 2 million jobs are estimated to remain unfilled due to the skills gap. 80% of manufacturers are already facing a shortage of qualified applicants for skilled or highly skilled positions. All the more reason for manufacturers to turn to emerging technologies that are transforming the manufacturing sector and also addressing these workforce issues.
1. Internet of things in manufacturing
A little-known fact about the Internet of Things is that it all started with a brown lipstick. Yes, you read that right. In the late 1990s, Kevin Ashton, a young brand manager in the UK, was curious to know why a certain shade of brown lipstick kept disappearing from store shelves in his local store. Intrigued by how the wireless network could pick up data on a credit card, he toyed with the idea of using this technology on products. He reasoned that a wireless network that could pick up data on a card, could also pick up data from a chip on a lipstick package. This way the company and the store would know exactly which lipsticks were on the shelves. And the idea of IoT was born.
The Internet of Things (IoT) is a network of physical devices that are embedded with sensors and, software that make them the “eyes and ears” in a vast range of use cases. From home automation (intelligent thermostats, connected doorbells, smart coffee makers) to industrial automation (electric vehicles, robotics, medical imaging) IoT is everywhere, talking to each other, receiving and sharing data amongst themselves without any human or computer interaction.
Internet of things in manufacturing is also called Industrial IoT. IIoT integrates various sensors, Radio Frequency Identification (RFID) tags, software, and electronics into industrial machines and systems to collect real-time data. Businesses then use this data to make measured, informed decisions to increase efficiency, streamline and simplify manufacturing processes, reduce downtime and costs, increase quality, and positively impact their bottom lines.
A perfect example to understand the importance of IoT in manufacturing is through predictive maintenance. The usual method for machine maintenance is to “run to failure”. Lengthy downtime for repairs is still considered unavoidable. With IoT, however, machines can be monitored remotely and maintenance teams can get a warning of potential faulty working and correct it in the early stages.
The manufacturing industry is leading the way in IoT with the market size for IIoT estimated to reach 110.6 billion U.S. dollars by 2025 (Statista).
IIoT in manufacturing holds great potential for
- Quality control
- Supply chain traceability
- Sustainable and green practices
- Overall supply chain efficiency
- Remote monitoring and predictive maintenance of machinery
- Asset management and tracking
- Inventory stocking
- Improved field service
- Facility management
Schindler is no longer known just for elevators capable of transporting passengers to their selected floor but its technology can now analyze and predict elevator demand patterns to reduce elevator wait times by as much as 50%.
2. Big data will be the fuel for growth
Every manufacturer uses data. However, there are various manufacturing software powering different solutions – ERP, MES, CMMS, manufacturing analytics. It is not easy to tie all the systems together to get the big picture about how the industry floor is performing. Industry 4.0 has already found the solution to this via big data.
Some examples of different types of big data in manufacturing are productivity data, sensors on machines and power consumption information from different machinery. It can also be integrated from outside partners or vendors. Big data in manufacturing becomes valuable only if one centralized view can be created. This is the “hub” into which all data must flow.
When data from all these systems are integrated, patterns can be found, and problems can be solved, efficiently and without complexity.
Big Data in manufacturing is not new, most manufacturers are already seeing the benefits in industries such as oil and gas, automotive, food and Beverage, refineries, plastics, and chemicals. GE was known for the manufacture of jet engines, locomotives, gas-fired turbines, and medical imaging equipment. Today it sells smart, connected versions of the same equipment and services founded on the massive data they generate.
Also read Machine Learning! Are Companies in India Ready for It?
3. Automation and Artificial Intelligence in manufacturing
We’re fascinated with robots because we see ourselves in them, they look like us and are programmed to think like us. Though a figment of the imagination, the Tin Man from Frank Baum’s The Wizard of Oz could have been the prototype for the first robot with artificial intelligence.
Manufacturers are already deploying automation on the factory floor as well as in their offices. We will continue to see the expanding usage of artificial intelligence in manufacturing for productivity improvements. AI will power demand planning, inventory planning, logistics and production scheduling.
Robots are taking on more complex traits using AI and machine learning to develop memory, increase dexterity, be more agile and effectively collaborate with each other and humans. These cobots (collaborative robots) are engineered to copy the actions of a human workforce and work in concert with humans, freeing factory workers from repetitive and dangerous tasks. So the manufacturing industry is increasingly looking to robots to shape their processes on the factory floor.
Read about: Robotic Process Automation vs Traditional Automation
4. Additive manufacturing or 3D printing
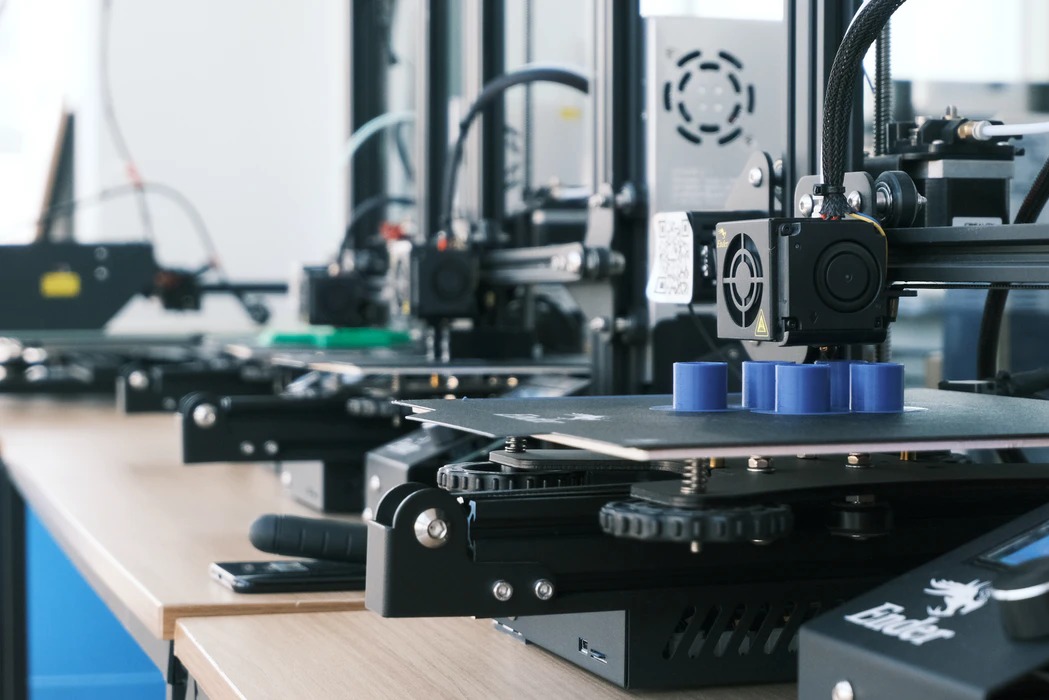
3 d printing actually dates back to the ‘80s when Charles Hull, a worker at a tabletop and furniture manufacturer, first patented the idea. Goaded by the length of time it took to create small custom parts, he developed an idea to take the company’s UV lamps and make a photosensitive resin, layer by layer to create custom parts. Buoyed by his success, he obtained a patent in 1986 and started his own company in California called 3D Systems.
3D printing is emerging as a valuable digital manufacturing technology. Already, more than two-thirds of US manufacturers use this technology to design products.
For manufacturing, 3D printing is emerging as a valuable digital manufacturing technology. Already more than two-thirds of US manufacturers use this manufacturing technology to design products, using less physical material, reducing product development costs, saving space, and creating malleable prototypes.
Additive manufacturing, so-called because it adds material in layers to create an object, uses CAD software or 3D object scanners for digitally 3 d printing machine parts. It deposits material in layers, in precise geometric shapes. Parts can then be stored as design files in virtual inventories to be produced whenever needed, which is known as distributed manufacturing. Transportation distances and costs are reduced and inventory management is simplified by storing digital files.
Today, additive manufacturing employs a huge range of possibilities from tooling to mass customization across industries.
5. Augmented Reality: Touchless Service Model
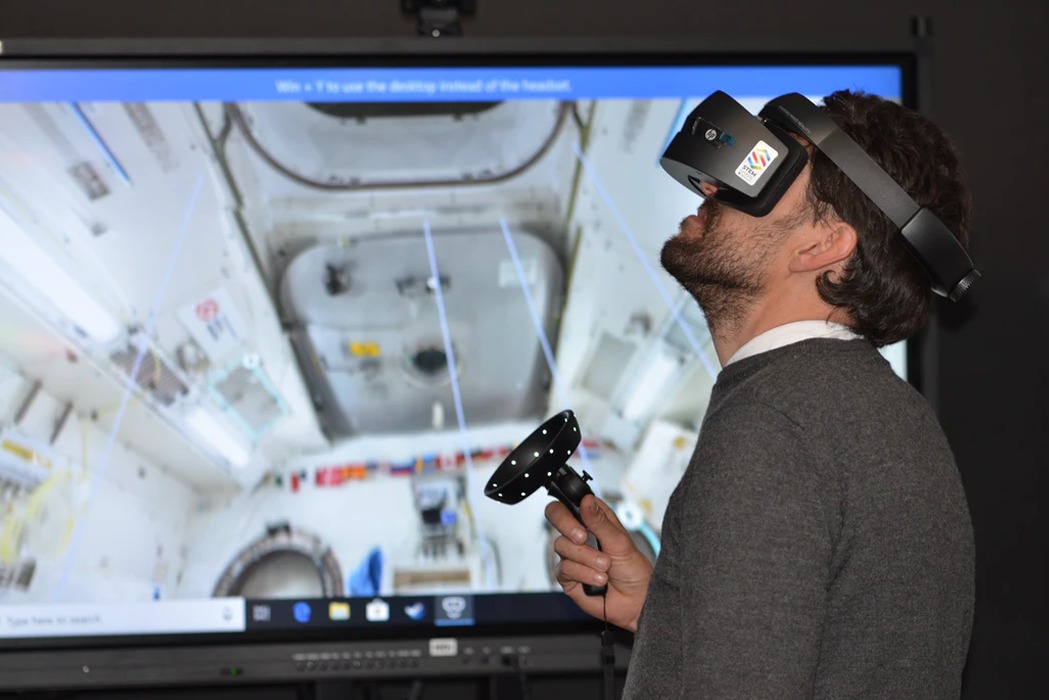
Forbes called 2019 the year virtual reality (VR) got real. This was the year Facebook’s standalone headset called Oculus Quest sold out in many locations a week after launch. Nintendo made an entry into the VR market with the Labo: VR kit for Nintendo Switch. Sony sold 4.2 million PlayStation VR (PSVR) headsets.
With the manufacturing sector beginning to explore VR, the potential for this manufacturing technology, in assembly processes, maintaining equipment and improved decision making is huge. For instance, factories could use augmented reality (AR) glasses to project data such as layouts, assembly guidelines, possible malfunction sites, or serial numbers for parts, enabling faster and easier workflows.
Simulated training using virtual reality in manufacturing can enhance training sessions with practical scenarios that show trainees how to perform tasks assigned to them or even what to do in an emergency situation such as a fire or a tornado.
AR and VR make it possible for maintenance technicians to carry out maintenance procedures from a remote location. These technologies also enhance efficiency by providing more significant insights and visibility to the multiple manufacturing processes.
These and other emerging technologies have significant implications for the manufacturing industry of today and tomorrow.